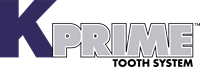
-
Equipment
Construction Equipment SolutionsWhether you're digging foundations or building communities, our reliable equipment delivers precision for construction work. Select from top brands like Komatsu, BOMAG, and Takeuchi, plus custom attachments to ensure you have the right tools for the job.Forestry Equipment SolutionsBalancing economic harvesting with sustainable forest management is key to preservation. With rugged, purpose-built forestry equipment from TimberPro and Komatsu, you can manage just that. Our team is ready to assist you no matter how remote your site is.Landscaping Equipment SolutionsDense urban areas can limit your ability to work efficiently, but our compact solutions from trusted brands like Takeuchi can help you navigate tightly confined spaces with the horsepower you require.Municipal Equipment SolutionsReliable equipment keeps communities running efficiently. Whether its for waste management, snow removal, or park maintenance, we supply trusted brands like Komatsu, BOMAG, and Takeuchi, with flexible warranties, on-site support, and smart technology to meet your needs.Surface Mining Equipment SolutionsSurface mining operations are increasingly complex. Whether you’re greenfield, brownfield, or fully operational, we have the equipment and technology solutions you need from the world’s leading brands like Komatsu — from haul trucks and dozers to loaders and more.Underground Mining Equipment SolutionsHelping meet the world’s need for resources requires reliable equipment and responsive support. With SMS Equipment, you’ll have a trusted partner that delivers both, by working together to maximize your productivity.Road Construction Equipment SolutionsIn the tough business of road construction, you need industry-leading heavy equipment products from trusted brands like Komatsu and BOMAG. Along with our on-site support teams, we’ll help you get your job done on time and on budget.Waste Management Equipment SolutionsWhether it’s for garbage compaction, landfill management, or transfer stations, we’re proud to offer purpose-built waste management equipment from BOMAG and Komatsu that meets your specific needs.Pre-owned Equipment SolutionsYou don’t have to buy new to get the job done right. We’re proud to offer pre-owned equipment from some of the world’s leading brands.RentalsAttachments of Every TypeWhether you’re looking for concrete pulverizers or harvesting heads, we’re proud to offer a complete range of attachments that meet your needs — as well as your standards.
-
Parts
Buy Parts OnlineWe provide support for all areas of your equipment, including powertrain, hydraulic systems, lighting, operator environment, undercarriage, electrical systems, cooling systems and more. Our network of parts and components is fully integrated between our branches and our manufacturers as well as with other distributors throughout North America.AttachmentsSMS Equipment holds a unique position in the industry as a one-stop supplier of the most complete range of attachments for your equipment.
We offer only world renowned brand names that meet your standards of reliability and productivity.
UndercarriageSMS Equipment has undercarriage repair centers that perform track pad swaps, turn pins and bushings, rebuild idlers, rollers and re-grouser track pads. We offer a practical management approach to ensure you achieve the best performance and durability from your undercarriage components.Ground Engaging SolutionsEven the harshest construction and mining conditions are no match for our ground engaging tools and parts. Optimize your operation with wear parts designed to endure, saving you both time and money.Consumable SolutionsFrom oils to filters to batteries, we have the consumables you need to keep your equipment running exactly as it should — including the expertise to keep you one step ahead.Safety EquipmentAt SMS Equipment, one of our core values is to care for each other without exception. We strive to set exceptional standards within our industries to demonstrate care for all internal and external stakeholders. We are proud to distribute and partner with business partners, providing you and your employees with exceptional safety products.Cost-Saving SolutionsSave big on our selection of clearance parts and attachments at drastically reduced prices. Let us help you find what you need, while keeping more money in your pocket.Current PromotionsPartnership pays off. Take advantage of our current limited-time promotions. -
Services & Support
Maintenance and Repair SolutionsOur range of maintenance and repair services will help you quickly get back on track. Whether emergency repair or preventative maintenance, in-shop or on-site, we will help keep your equipment working exactly as it should.Rebuilt SolutionsYour equipment should be designed with your operation in mind. Let us show you what’s possible with our rebuilding and remanufacturing capabilities that build custom equipment solutions tailored to your specific operational goals.Training SolutionsInvest in your job site safety and productivity with the right training and support from our world-class specialists. From best practices to emerging technologies, we’ll make sure your team has everything they need to work safely and efficiently.Warranty SolutionsOur partnership comes with peace of mind. With comprehensive warranties on equipment and components, we’ve got you covered so you can rest easy knowing your investment is secure.Financing SolutionsEnjoy the flexibility of financial options that meet your needs. With competitive rates in both Canadian and US dollars, and rent-to-purchase options, we’ll work with you to determine the best financing solution for your business.Fleet ManagementCurrent PromotionsPartnership pays off. Take advantage of our current limited-time promotions.
-
Technologies
Technologies by IndustryNo matter your industry, technology will help you work both safer and smarter. Our technology experts will help you discover the latest advancements for your industry and operation.Technologies by NeedAdvanced technologies can be the solution to your specific needs. Whether it’s decarbonization, safety, labour shortage or productivity, our technology experts will help you discover the possibilities.Technologies by SolutionDiscover the variety of solutions made possible with new and emerging technology. From telematics to autonomous haulage to machine control, our technology experts will help you find a smarter and more efficient way to get it done.
-
News & Resources
News & ResourcesStay ahead by being in the know with SMS Equipment news and resources. Discover trends, expert insights and latest developments that affect you and your business.
-
Company
CareersAt SMS Equipment, we’re more than machines. Join our team of world-class specialists and build your career with us. Explore our open positions near you and across the country.Branch LocationsConnect with us and explore the possibilities. Visit us at any of our branch locations across Canada and Alaska or give us a call. We look forward to hearing from you.About UsThe right partnership makes everything possible. See what sets us apart as a collaborative growth partner committed to your success with comprehensive solutions unique to your operation.News & ResourcesStay ahead by being in the know with SMS Equipment news and resources. Discover trends, expert insights and latest developments that affect you and your business.